Total Quality Management
Organizational Excellence
Total Quality Management (TQM) is an approach that seeks to improve quality and performance which will meet or exceed customer expectations.
You can achieve this by integrating all quality-related functions and processes throughout your company.
Questions to ask
- Why should your company bother implementing Total Quality Management (TQM)?
- Isn’t TQM an old idea that has outlived its usefulness?
- Why bother breaking down each process and creating a lot of documentation?
- With virtual offices, webinars and go-to-meetings, why bother learning retro quality management tools like brainstorming, fishbone diagrams and statistical process control (SPC)?
The answer to these questions is simple. TQM looks at the overall quality measures that your company can use, and they include managing quality design and development, quality control and maintenance, quality improvement, and quality assurance.
Which Parts of Your Business Require TQM?
We can implement TQM successfully in any part of a business, including:
- Accounting
- Finance
- Maintenance
- Field servicing
- Manufacturing
- Sales and marketing
- Materials management
- Legal and administration
- Research and development
How is TQM Relevant to Your Business Today?
TQM may be an old idea, but the processes and results are just as valid today. In a slow and an uncertain economy, your company cannot afford product defects, downtime, lost opportunities, lost customers and revenue due to poor quality and service. You can apply the principles of TQM because they as still effective today.
- TQM Focuses on Your Customers
Total quality management’s goal is to meet and exceed customer expectations. They involve the customer to define expectations and quality standards. Every person and department in the company is focused on its part in the customer service process.
- TQM Focuses on Your Employees
With high unemployment and job uncertainty, your employees may be disengaged and their morale may be low. TQM emphasizes employee involvement at every level, working in quality teams using a defined process to solve problems. Employees are empowered and motivated to participate in the planning, implementation and review of the quality process since they have a stake in the outcomes.
- TQM Reduces Costs
While there is an initial cost in training, process development, controls and measurement standards, the return on the investment can far exceed the investment. Improved customer satisfaction, defect and cost reduction, increased revenues and improved employee morale are the results of an effective TQM culture.
However, TQM also requires a significant training period for those employees involved in it. Since the training can take people away from their regular work, this can actually have a negative short-term effect on costs.
Also, since TQM tends to result in a continuing series of incremental changes, it can generate an adverse reaction from those employees who prefer the current system, or who feel that they may lose their jobs because of it.
TQM works best in an environment where it is strongly supported by management, it is implemented by employee teams, and there is a continual focus on process improvement that prevents errors from occurring.
There are a number of tools available to assist in a TQM effort, such as:
- Benchmarking
- Failure analysis
- Plan-do-check-act (PDCA) cycle
- Process management
- Product design control
- Statistical process control
It's your turn
Do you want to apply total quality management in your business? What is your experience with total quality management? Contact us today for a free consultation and our Business Improvement Experts at Tianlong Services will show you how to use TQM to achieve that goal.
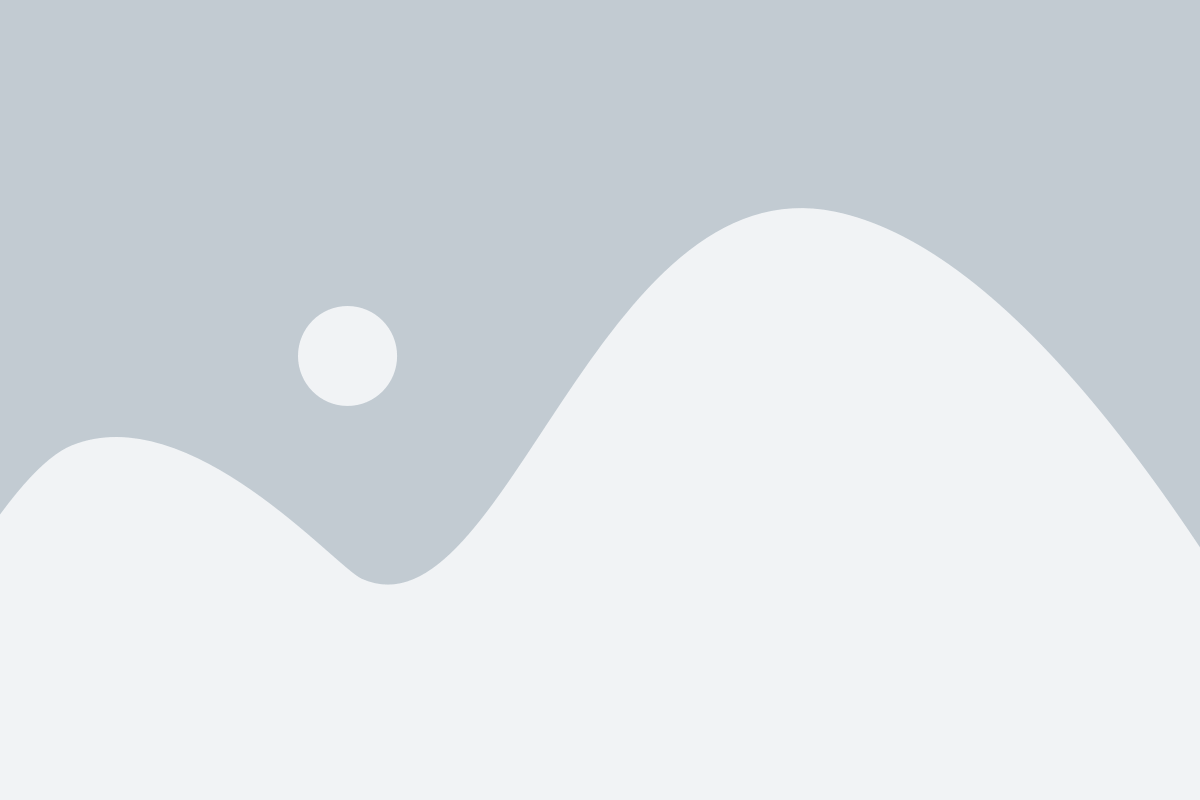
No Obligation
Request a free trial
You will get a month’s worth of bookkeeping. Whether or not you continue with us, your reports for the month are yours to keep.